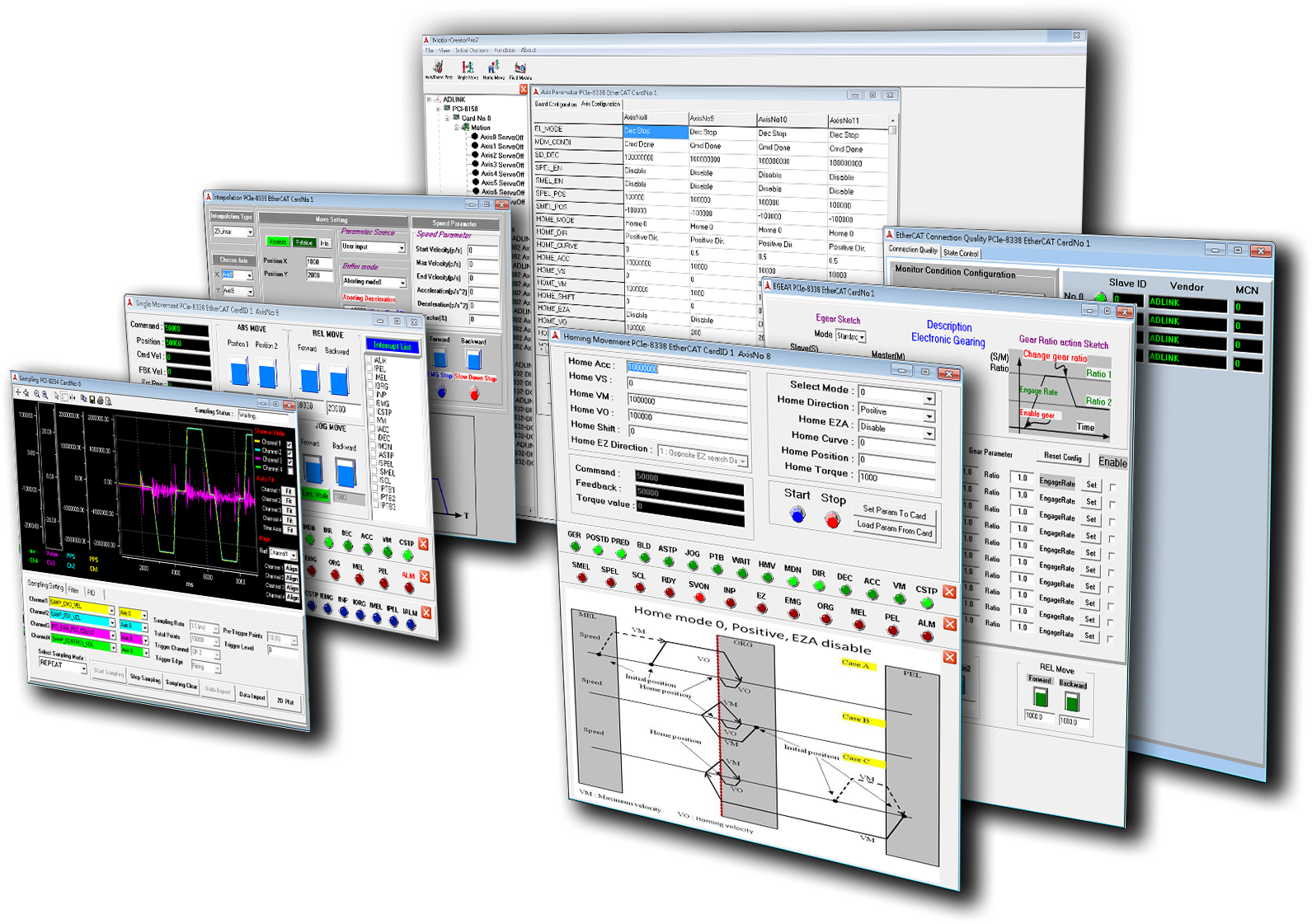
APS SDK- Automation Product Software SDK
ADLINK’s All-in-One solution for automation

Spirit of Motion Control, Designed for Machine Automation
The Automation Product Software SDK (APS SDK) is an all-in-one solution with an optimized uniform interface to access all supported ADLINK machine automation products. The APS SDK features rich, powerful application-oriented motion functions that co-work with components such as system platform management, field bus communications, general digital input/output, general analog input/output and support for various counters/timers. With ADLINK machine automation series products that support APS SDK, machine makers can build and deploy applications easily and quickly with a universal tool, saving on TCO and enabling faster time to market.
-
More than 15+ motion and 30+ I/O products benefit from the rich built-in functions of APS SDK
-
APS Library reduces operational complexity and development period
-
Universal and intuitive interactive configuration via the MotionCreatorPro2 visualization utility
-
Hardware and OS independent with consistent programming style
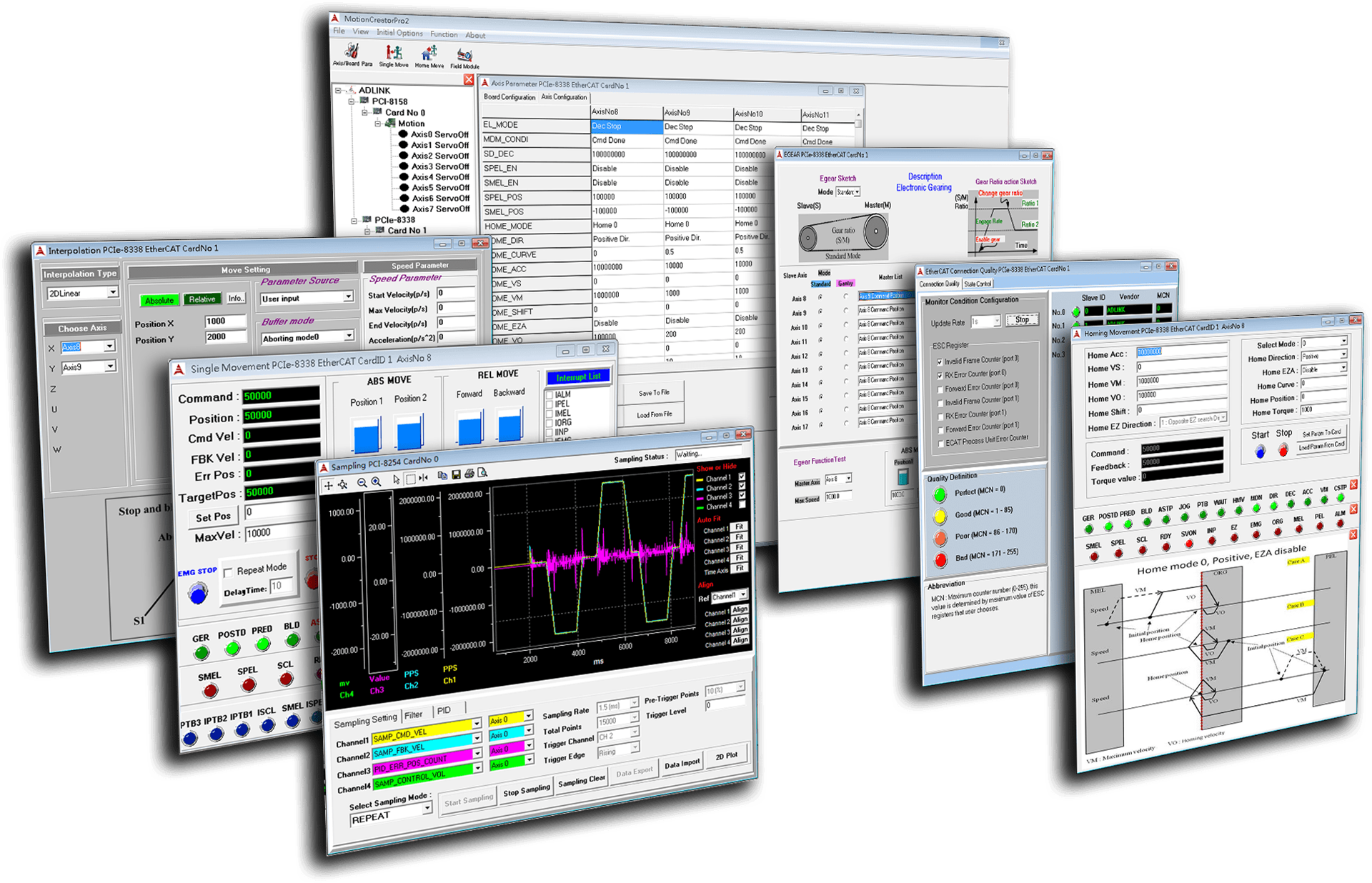
APS SDK
Automation Product Software SDK (APS SDK)
- ADLINK automation product drivers
- APS Library
- Motion Function (T/S-Curve Velocity Profile, Interpolation, etc.)
- Application Function (Position Comparison and Trigger Out, etc.)
- Advanced Controller (PID Plus Feedforward Gain Control, etc.)
- MotionCreatorPro2
- ADCNC Library
APS SDK Architecture
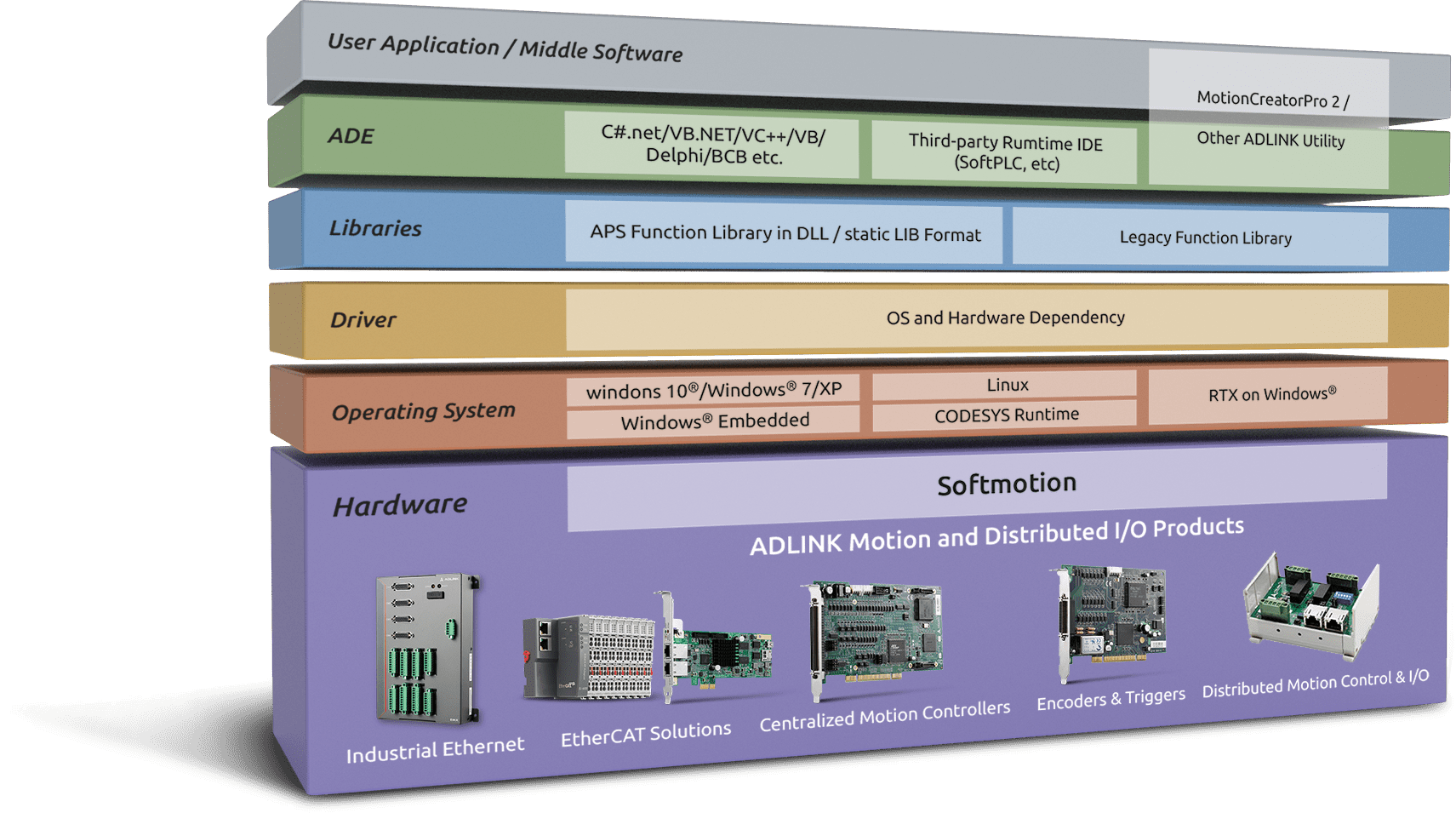
Use Cases
-
-
01
Equidistant Spiral Motion Solution -
ADLINK 3D Equidistant Spiral Motion Solution Reduces Material Costs
-
-
-
02
2D Error Compensation Technology -
ADLINK’s 2D Error Compensation Technology Effectively Improves the Precision and Accuracy of Wafer Inspection
-
-
-
03
Velocity Planning Solution -
ADLINK’s Velocity Planning Solution Maintains Motor Stability During Laser Beam Machining
-
-
-
04
Multi-point Comparison Solution -
ADLINK's Single Latch Activated Multi-point Comparison Solution
-
Universal Visualization Utility Delivers Easy Configuration
The APS SDK includes the easy-to-use MotionCreatorPro2 configuration utility, allowing users to tune device performance and verify control results and hardware functions without the need for coding, via a universal visual interface, reducing effort from product testing to system development and debugging, and delivering faster and easier deployment.
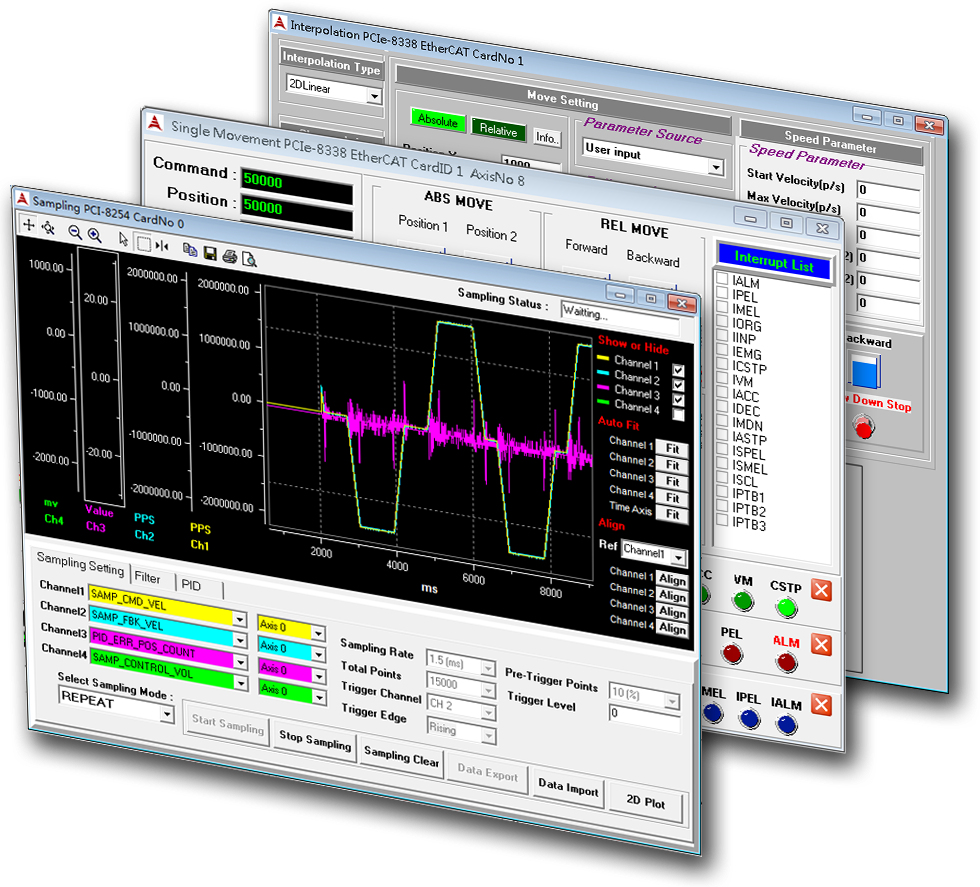
Freedom from Hardware, OS and Programming Language Variability
APS SDK is a complete package which includes a variety of OS device drivers. Using a single function library, users can operate ADLINK motion products in a simple and consistent way, without the need to reprogram when adding or removing different types of devices in a wide range of operating systems. Moreover, the APS library also provides various programming language interface and examples for users, including ANSI C/C++, Microsoft Visual C/C++, Visual Basic, C#, Visual Basic.NET, Borland Delphi, and C/C++ builder, meeting the needs different users and use cases for machine development.
Rich Function Library Speeds Up Automation Application Development
Leveraging ADLINK’s 25 years of experience in machine automation, the APS SDK provides a rich function library with a range of general, advanced and application-ready motion functions to help developers dramatically reduced development and maintain costs and lower the technical threshold of manufacturing automation applications.
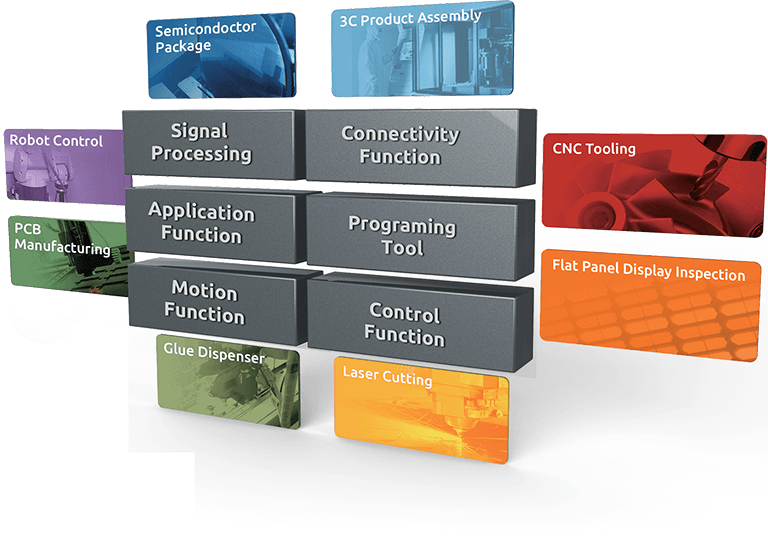
Powerful Motion Kernel
Drives Smart Machine in Smart Factories.
ADLINK Softmotion provides a variety of dependable motion controls, based on an efficient algorithmic kernel featuring basic motion functions such as point-to-point and interpolation, but also variant vertical functionality for AOI, laser cutting, and semiconductor management, and even robotic control. High precision and speed, together with enhanced synchronous motion control, make ADLINK Softmotion a key player in reduction of operational complexity and development period for a wide variety of industrial applications. Compatibility with numerous I/O connection types, Softmotion delivers maximum synchronization between motion and I/O control, vastly improving application throughput.
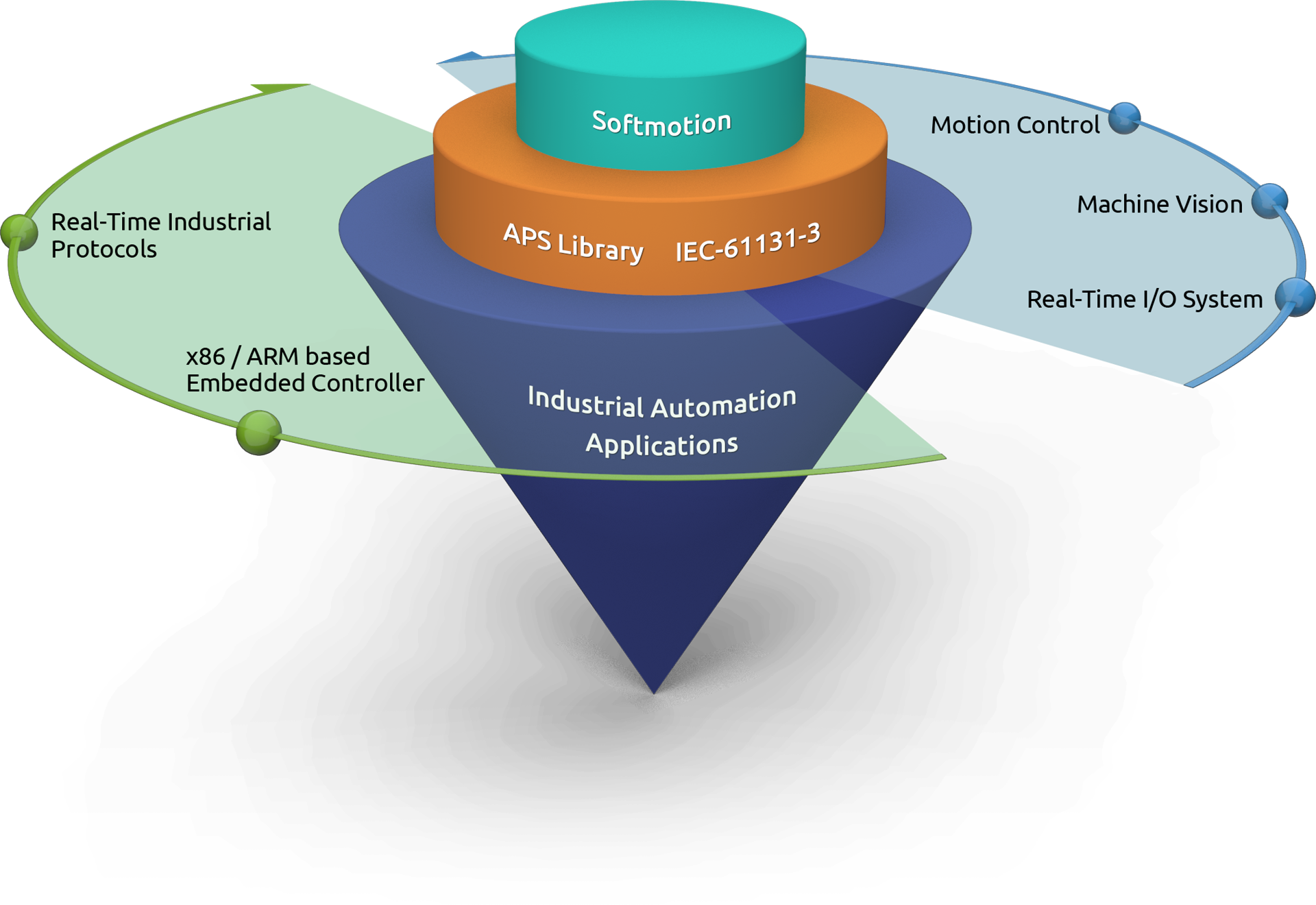
APS Library Key Features
Motion Functions
-
Home Return Modes
To ensure motion repeatability, the mechanism must reset to the zero-position via the dedicated sensor point “ORG”, normally completed by combining “ORG”, “EL” and “Index” signals.
-
Position Override
After movement begins, the position target can be changed on-the-fly even if the motion reaches maximum velocity.
-
Spiral Interpolation
If the start point and destination of a circular interpolation movement lie on different planes, a Spiral function is required to directly regulate the movement.
-
Speed Override
Changes rotation speed on-the-fly while the axis is running.
-
T-Curve / S-Curve Velocity Profile
Acceleration and deceleration times are programmable, and rates can be set individually, with S-curve motion compensating for generated mechanical vibration.
-
Linear and Circular Interpolation
To complete multidimensional motion, any 2, 3, or even all 6 axes are required for linear interpolation and any 3 axes can execute circular interpolation.
-
Continuous Move (Contouring)
Continuous movements comprise a range of linear and circular interpolated paths. Point-Table functions support hundreds of paths to smooth the velocity of continuous movement supported by included velocity planning software..
-
Synchronization
Simultaneous start/stop can be executed on multiple axes in one card, or multiple axes across multiple cards, using software or external input signals. This feature is especially beneficial for complicated motion patterns requiring absolute synchronization of multiple axes.
-
Path Blending
Anticipating sharp corners and small arc path execution, path blending is required to decelerate automatically and ensure smoothness of the velocity at junctions of two linear paths.
-
Velocity Planning
Velocity planning is required to smoothly implement continuous movement and reduce vibration. The velocity of each path is generated automatically according to corner angles of complete paths.
APS Library key features
Programming Languages
-
IEC 61131-3
The third section of the open international standard IEC 61131 for programmable logic controllers, CODESYS (provided by 3S enterprise) is integrated into specific ADLINK motion controllers.
Controls
-
PID Plus Feedforward Gain Control
All servo applications require specified safe and stable PID loop parameters in order to perform position control, ADLINK Softmotion provides a proportional-integral-derivative (PID) algorithm with adjustable acceleration and velocity and feed-forward gain to simplify servo application development..K
-
Auto-tuning
In order to reduce tuning efforts and acquire accurate PID parameters, auto-tuning applications are provided in ADLINK dedicated software, allowing conditions to be configured according to real application requirements.
APS Library key features
Application Functions
-
Electronic Gearing
To implement multi-axis synchronization, this function sets a ratio between multiple slave axes and one master axis to simplify mechanism. One example is a system where two rotating drums turn at a given ratio to each other.
-
Pitch Compensation
Irrespective of the type of ball screw system used, there always exists the non-linear section of the whole ball screw that affects the accuracy of overall motion. This function compensates for pitch error in real time.
-
Position Compare & Trigger Output
Up to 20MHz encoder input frequency, hardware-based high-speed position comparison, and trigger output, ideal for AOI applications.
-
Encoder Event
To accelerate the throughout of entire motion system, the encoder event is used to triggers other axis movement immediately when the target axis achieves the planned position.
-
Automatic Backlash Compensation
Upon direction change, outputs backlash corrective pulses before sending commands. This function only supports single-axis movement.
-
PWM Generation
In general PWM generates pulse up to 25MHz with either fixed frequency or fixed duty-cycle modes, and is suitable for laser, and dispensing applications.
-
Position Latch
The latch function captures the instant counter value of one certain axis when the latch signal activates. The LTC channel is used to receive the latch pulse and the latch function is implemented with hardware.
Other Features
-
DSP
Digital Signal Processing allows time-critical motion control, multiple axis synchronization, and standalone control in a variety of applications.
-
Hardware Emergency Input
A safety protection feature providing emergency shutdown in case of malfunction.
-
Manual Pulsar Input Interface
Some motion control solutions provide an interface that connects manual pulsar input devices, which can be used to move the axes.
-
Analog Output / Analog Input Channels
Some products offer analog output/input channels for voltage signals.
-
Digital Encoder Input
Most feedback signals can be classified as digital pulse types consisting of A, B phase and index signals. Normally the frequency of digital encoder can be supported up to 20MHz (@4xAB phase).
-
Diagnostic
The EtherCAT-network error diagnostic tool which can detect communication packet and network topology status. Users can check network status immediately, and find the bad network stations for their topology, reducing troubleshooting time.
Connectivities
-
Ethernet Connectivity
Considering the cost and flexibility of overall automation equipment design, Ethernet connectivity allows localization of movement or I/O modules to save space and extend control through adding the modules.
-
Field Bus Connectivity
Field Bus Connectivity localizes motion of I/O modules to save space and extend control through addition of modules, with dedicated I/O and Motion provided as “HSL” and “MNET” respectively.
-
EtherCAT Connectivity
EtherCAT supported is a variety of connection topology methodologies, including star, tree, and ring types. As a result, EtherCAT offers unified, powerful communication for the entire automation sector, ensure quality.